Kırma Eleme Tesisinde Agrega Olarak Kullanılan Kayaçlar Nelerdir ?
Dünyada ve ülkemizde kırma taş ( agrega ) üretiminde kullanılan kayaçlar genellikle kalker- kireç taşı, dolomit, bazalt, andezit, granit ve dere malzemesi vb. ‘dir. Kayaçların jeolojik ve yapısal özelliklerinin birbirinden farklı olması nedeniyle tesiste kullanılacak ekipmanlar farklılık göstermektedir.
Kayaçların Mohs sertlik skalasındaki değerleri, Los angeles değerleri, kırılganlıkları, basınç dayanımları, kimyasal analizi vb. özelliklerine göre makine ekipman seçimi yapılır. Kireç taşı, kumtaşı, granit, bazalt vb. farklı kayaçlar için, aynı özellikte kırıcı aksam ve aksesuarları kullanılmamalıdır. Kalker için üretilen kırıcının dökümleri ve bazalt için üretilen kırıcının döküm ve aksamları farklıdır. Uğur Makina kayacın özelliklerine göre uygun aksamları geliştirerek imalatını üstlendiği kırma eleme tesislerinin işletme maliyetlerinin asgari düzeyde olması için çalışmaktadır. Örnek olarak kayaçlardan kalker ve bazalt için detaylar aşağıda açıklanmıştır.
Kalker (Kireç taşı ) ;
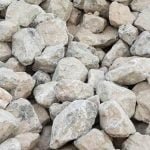
kalker
Sedimanter ( tortul ) kayaç grubuna dahildir. Kirecin ham maddesi olan kireç taşı veya kalker, genellikle kalsiyum karbonat (CaCO3) dan oluşur. Genellikle beyaz renklidir. Mohs sertlik değeri 3- 3.5 civarındadır. Malzemeye yapılan XRF analizinden sonra Mg içeriğine göre dolomit olarak adlandırılabilir. Sedimanter kayaçlar daha önce oluşmuş kayaçların parçalanması, taşınması, çökelme ortamlarında biriktirilmesi ve taşlaşmasıyla oluşabildiği gibi, geçmişte yaşamış organizma parçalarından da oluşabilir. Bu kayaç grubu genellikle tabakalı bir yapıya sahiptir. Kalker tesislerinde genellikle primer çeneli veya darbeli kırıcılar, Sekonder darbeli kırıcılar, tersiyer darbeli kırıcılar ve dik milli kırıcılar seçilerek talebe uygun tesisler tasarlanmaktadır. Kırıcı aksamlarında ( palet, astar vb. ) genellikle mangan alaşımlı dökümler kullanılmaktadır.
Bazalt ;
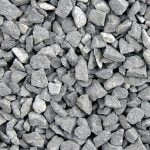
bazalt
Magmatik kayaçlardan volkanik yüzey kayaçlar grubuna dahildir. Siyah renkte ve kesif yığınlar halindedir. Doğada kütle, damar ve akıntı halinde bulunur. Mohs sertlik değeri 5.5 – 6.5 civarındadır. Magmatik kayaç olması nedeniyle yüksek oranda silisyum içermektedir. Dolayısıyla aşındırıcılığı oldukça yüksektir. Bu sebeple kırıcı aksamlarında ( palet, astar vb. ) krom alaşımlı dökümler tercih edilmektedir. Bazalt tesislerinde sert ve aşındırıcı olması nedeniyle primer çeneli kırıcılar, sekonder konik kırıcılar ve sekonder çeneli kırıcılar, tersiyer kırıcı olarak da dik milli kırıcılar seçilerek talebe uygun tesisler tasarlanmaktadır. Ayrıca tüm tesiste aşındırıcılığın yüksek olması sebebiyle malzemenin akış yüzeyleri hardox astar ile kaplanmaktadır.